It’s been a week since we were meant to depart from San Diego en route to Martinez, and while I’m still disappointed that we had to make that call, we now know that it was definitely the right call to make. I’ll look forward to Festina Lente arriving in Martinez sometime mid-October now.
Upon learning that we’d not be departing Sunday, my primary concern was where I would leave Festina Lente after September, as the slip was only rented through then. I had originally made arrangements with the seller to make use of a mooring ball if I needed more time in San Diego before delivery, but when it looked as though everything was going smoothly for a September passage, we stopped keeping that option open. I feel really stupid for not insisting on holding on to the mooring ball as part of a contingency plan. Thankfully, albeit expensively, I was able to extend our stay in her current slip through October. That was a huge relief. Alternative plans included sailing her down to Mexico in search of a temporary mooring!
The decision not to go also meant that I would not be able to participate in the delivery due to time constraints and family/work obligations. Now that I would no longer be aboard for the passage, I suddenly had a lot more to do in preparation for the delivery before I could leave the boat. The delivery captain will need information that I had anticipated being able to either discover together or to convey to him verbally as-needed. Since I won’t be aboard, I need to anticipate the need for this information ahead of time and document it.
But first, I took a bit of a pity day to let me process the disappointment of not being part of the passage. I stuck to work I considered to be more “fun” or at least relaxing.
This included applying the vinyl lettering I had cut out using my Cricket cutter prior to heading to San Diego. The sellers hadn’t put the name of the vessel or hailing port on the transom after repainting the hull because they knew she’d be up for sale. After researching what vinyl is most recommended for use on boats, I decided it made sense for me to cut my own to save a few bucks. I learned a lot of great tips along the way, and for a first attempt performed while floating around on the dinghy with nobody around to help I feel I did a good job, but the reality is that I totally botched it and will need to re-do it once the boat is in Martinez. It’s good enough to get her up here, though.
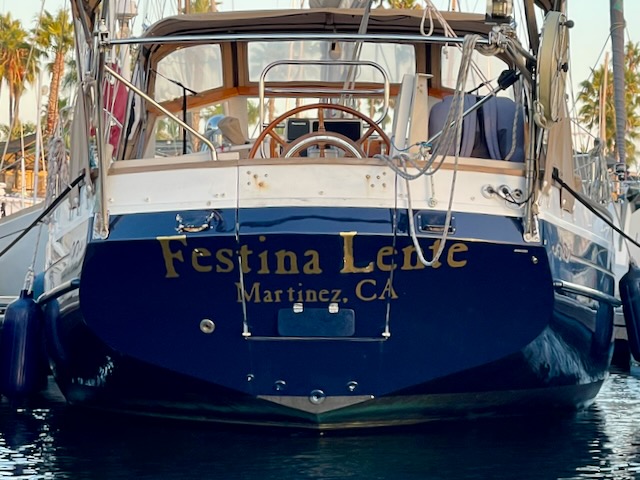
The second fun job was making sure the dinghy and its motor were operational. This involved firing up the motor and taking an enjoyable cruise around the harbor at sunset.
The final job I chose to take on for Saturday was making the dinghy davits work better. When a fellow employee helped me take the boat to the pump out station a few days prior, I found that it was way more challenging to hoist the dinghy up than it ought to have been. Upon investigation I found that one of the lines was severely chaffed and had a hard time running through the sheaves, one of the blocks was completely seized up and part of the davits itself was bent such that the sheaves within couldn’t turn freely. I replaced the line and the seized block and attempted to correct the bent davits, but that part proved more than I could handle on my own. Still, it’s now much easier to hoist the dinghy. Until I’m able to get the bend fixed properly, I may try sanding the edges of the sheaves to allow for more clearance.
On Sunday, I began performing a full inventory of the boat and sketching out all components of critical systems. This involved a lot of contorting myself into awkward positions while I peered through hatches and ports that aren’t intended for daily use. One of the things that really pleased me was to see just how clean the portions of the boat you don’t see are and how great a job the previous owners did taking care of Festina Lente.
Sunday afternoon involved a shakeout sail. The fellow employee mentioned above brought his family along and two additional employees joined us on a short sail out to the ocean. While it was fun, it also provided an opportunity to make sure that equipment that is critical for the upcoming passage was operating correctly. Of primary importance was the engine and autopilot, both of which did a great job.
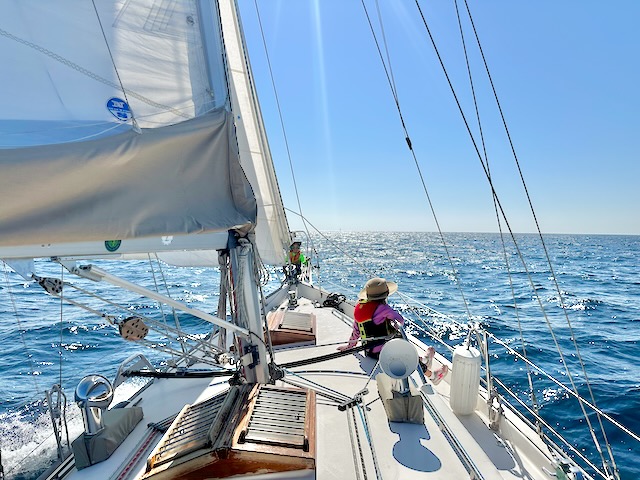
Several of us took turns at the helm, including a boy who was a very good helms-person. He demonstrated knowledge of how to use the radar to determine obstacles, paid attention to oncoming traffic, and responded well to some of the unpredictable things that happen in somewhat crowded channels.
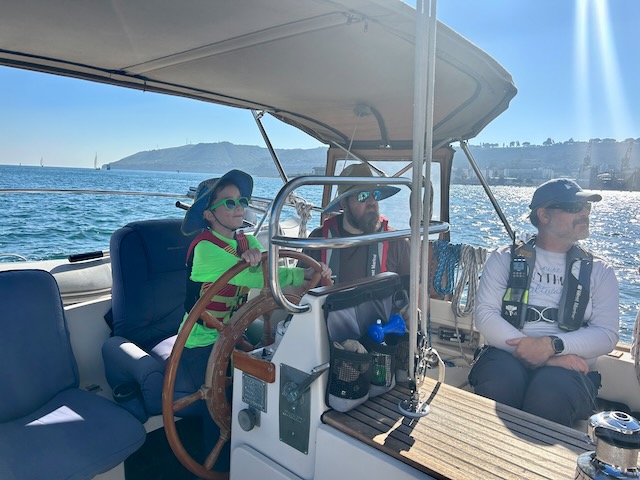
Getting back into the slip was a bit chaotic and had some close calls, but we managed to dock unscathed (and not having scathed anything else). I learned some important lessons about the need to communicate expectations more clearly.
Once my guests had left, I returned to working on the boat. Since the engine oil was now warm, I took this opportunity to change the oil. This was another learning opportunity. I had a hand pump available, but it took me a while to figure out the best way of connecting so that I could maximize the pump’s ability. Several hours later, I still don’t think I managed to fully drain the sump, but it’s also possible that the volume of the sump doesn’t match what’s in the original Westerbeke documentation. During this time, I also discovered why the air pressure instrument that hangs near the galley isn’t fastened properly: the companionway stairs bump into it every time the stairs are lifted. I’ll need to either sand off some of the stairs or relocate the instrument.
When Monday came, it dawned on me just how little time I had to finish preparing, and I started to feel a bit overwhelmed. I had a productive morning that involved continued organizing and inventory of the boat as well as a couple visits to the fuel dock to get 30 gallons of additional diesel for the passage.
All of my morning momentum was completely lost once I tried to figure out how to hoist the dingy motor off of the dingy and onto the davits. I made so many failed and very sketchy attempts before finally finding the best point to attach the motor to the block and tackle so that I’d be able to hoist it high enough to clear the davits and to maintain control over positioning. Next time will be easy, but I wasted a lot of time this first go.
As the light started to fade, I moved on to interior projects. Because the boat will be left alone in San Diego for a while, I wanted to make sure I installed the BRNKL security system before I left. This also provided an opportunity to familiarize myself with some of the electrical system. For now, I just have basic monitoring in place, but it’s enough to have peace of mind while away from the boat.
Tuesday was an all-out mad dash to finish up the inventory, pack my bags, get the rental car, unload the boat, shut down all the things, close all the seacocks and hit the road back to Martinez. Because I had brought a rental life raft down with me, flying back wasn’t an option. I managed to avoid LA traffic for the most-part, but still had a late arrival. I got in around 10:40pm.
The new plan is to have the delivery captain and his mate bring Festina Lente up to Martinez without me some time in mid-October. In the meantime, I need to work on preparing documentation reflecting the notes I took when inventorying, etc.